Hose Testing
At Flextech we take the safety of our customers, staff and general public very seriously. Hoses under pressure can fail in service causing severe injury if they are not correctly assembled or installed. It is for this reason that we have destructive and non-destructive testing procedures to ensure the integrity of each hose under pressure.
Hose Pressure Testing: Ensuring Safety and Reliability
At Flextech, we take pride in delivering premium hose assemblies that guarantee optimal performance, safety, and longevity. Our commitment to excellence is underscored by our rigorous hose pressure testing process, which plays a pivotal role in maintaining the highest standards across all our products.
Why is Hose Pressure Testing Essential?
Hose assemblies are vital components in numerous industries, ranging from food and beverage, automotive to energy, and aerospace to pharmaceuticals. As these applications often involve conveying fluids or gases under high pressure, any compromise in the integrity of the hose could lead to catastrophic consequences, including leaks, bursts, system failures or operator or consumer health and safety.
Our hose pressure testing serves as a crucial quality assurance measure, meticulously assessing the strength and durability of our hose assemblies before they reach our esteemed customers. By subjecting our products to stringent pressure assessments, we ascertain their capability to withstand the most demanding operating conditions, ensuring peace of mind for our clients and their valuable assets.
What Does Flextech Do To Keep You Safe?
Flextech operates a technologically adept automated pressure testing equipment system that is capable of running bespoke test cycles with recorded test results to ensure safety and peace of mind. Leaking hose assemblies are not only a risk to employee health and safety but also there is an increased risk of environmental contamination and costly production losses due to downtime.
At Flextech we operate a number of different hose testing procedures to satisfy the requirements of hose assemblies for their bespoke applications.
Unravelling the Hose Pressure Testing Process
1. Pre-Test Inspection: Before initiating the pressure testing, our team examines each hose assembly for any visible defects, irregularities, or potential weaknesses. This step enables us to rectify any issues proactively, guaranteeing the most reliable and accurate test results.
2. Controlled Pressurisation: During the pressure testing phase, we apply precise and controlled pressure to the hose assembly. The pressure is gradually increased, simulating real-world conditions to assess the assembly's resilience and leakage resistance.
3. Leakage Detection: Equipped with sensitive instrumentation, we're able to detect leaks in the hose assembly. This ensures that no potential defect goes unnoticed.
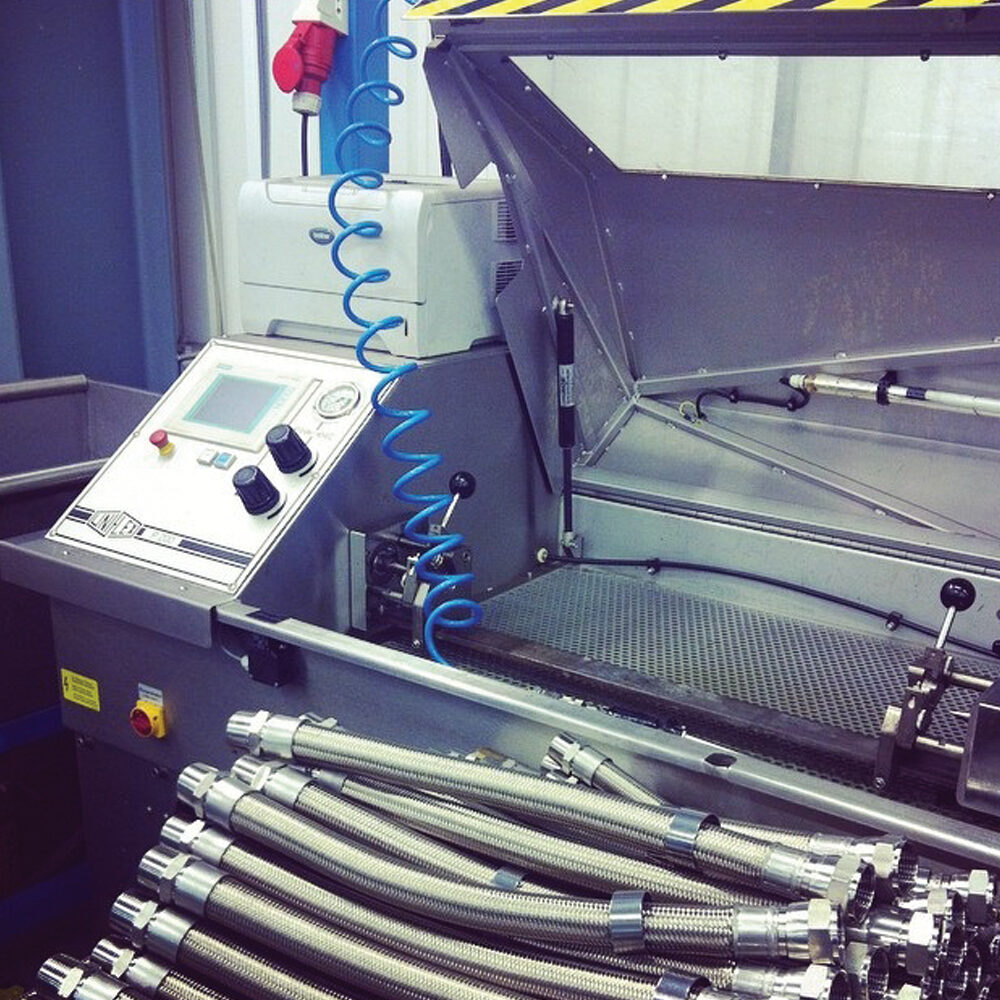
4. Endurance Testing: In addition to assessing the immediate performance under pressure, we can also conduct endurance testing, wherein the hose assemblies are subjected to extended periods of pressure exposure. This evaluation provides valuable insights into the assembly's long-term durability, crucial for applications demanding sustained operational excellence.
5. Data Analysis and Reporting: We are able to provide our clients with in-depth insights into the performance of their hose assemblies.
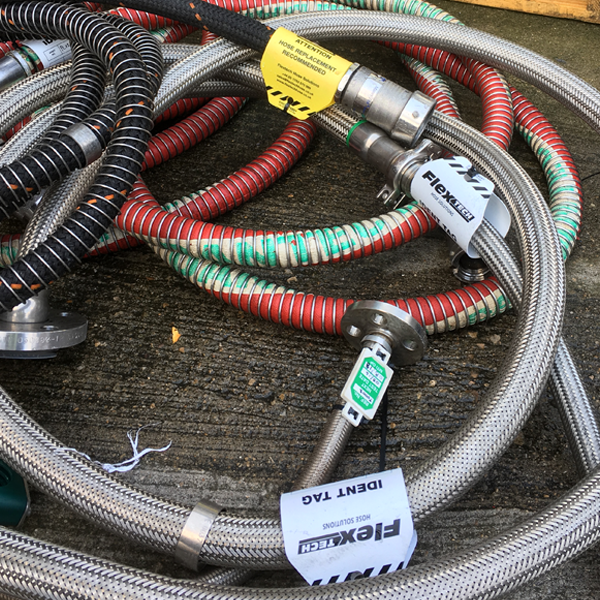
Types of Testing
Hydrostatic Hose Testing
Hydrostatic hose testing is a fundamental process in our comprehensive quality assurance regime. During this procedure, our technicians subject the hose assemblies to pressurised water to assess their ability to withstand the designated pressure levels without leakage. This method allows us to pinpoint potential weaknesses or vulnerabilities in the hose assembly that could compromise its integrity under high-pressure scenarios.
The hydrostatic testing procedure not only guarantees that our hose assemblies can handle the specified pressure safely but also aids in identifying any potential defects that might have occurred during the manufacturing process.
Air-under-water Testing for Hose Leaks
In our commitment to deliver the highest quality hose assemblies, we can conduct air-under-water testing. In this process, the hose assemblies are pressurised with air while submerged in water, enabling us to detect even the tiniest leaks that might otherwise remain undetectable through conventional means.
The air-under-water testing is a highly sensitive technique, allowing our team to identify potential irregularities, or micro-cracks that could compromise the hose assembly's integrity therefore providing a reliable and safe solution for our clients' critical applications.
Electrical Continuity Test
The electrical continuity test is a critical examination carried out on our hose assemblies and connections to verify their static dissipative properties and resistance. As many industries deal with sensitive equipment or inflammable substances, ensuring safe electrical conductivity is of utmost importance.
We assess the electrical continuity of the hose assemblies accurately through a test which determines whether the hose maintains a secure electrical path and effectively dissipates static charge to prevent the risk of electrical sparks, which could be hazardous in certain environments.
By conducting this test, we are able to provide our clients with an added layer of safety and confidence in our products. Where necessary, our hose assemblies are designed not only for their exceptional mechanical properties but also for their ability to mitigate electrical risks, making them a trusted choice for applications where safety is paramount.