Our Hose Design and Manufacturing Method
Our Hose Design and Manufacturing Method
Every application is unique. From designing to manufacturing, we create the bespoke hose assemblies that convey materials for applications such as food, beverage, pharmaceutical, water, air, fuel, chemicals and much, much more.
Flextech is Here to Help
Flextech specialises in finding the solution to a hose problem rather than just simply selling the cheapest product because in our world having a fit for purpose hose solution is everything. When investigating a problem you may find a good hose used in the wrong application which can be a costly disaster. For this reason, our prime objective is to help you to make the right choice and then follow it through with detailed technical support.
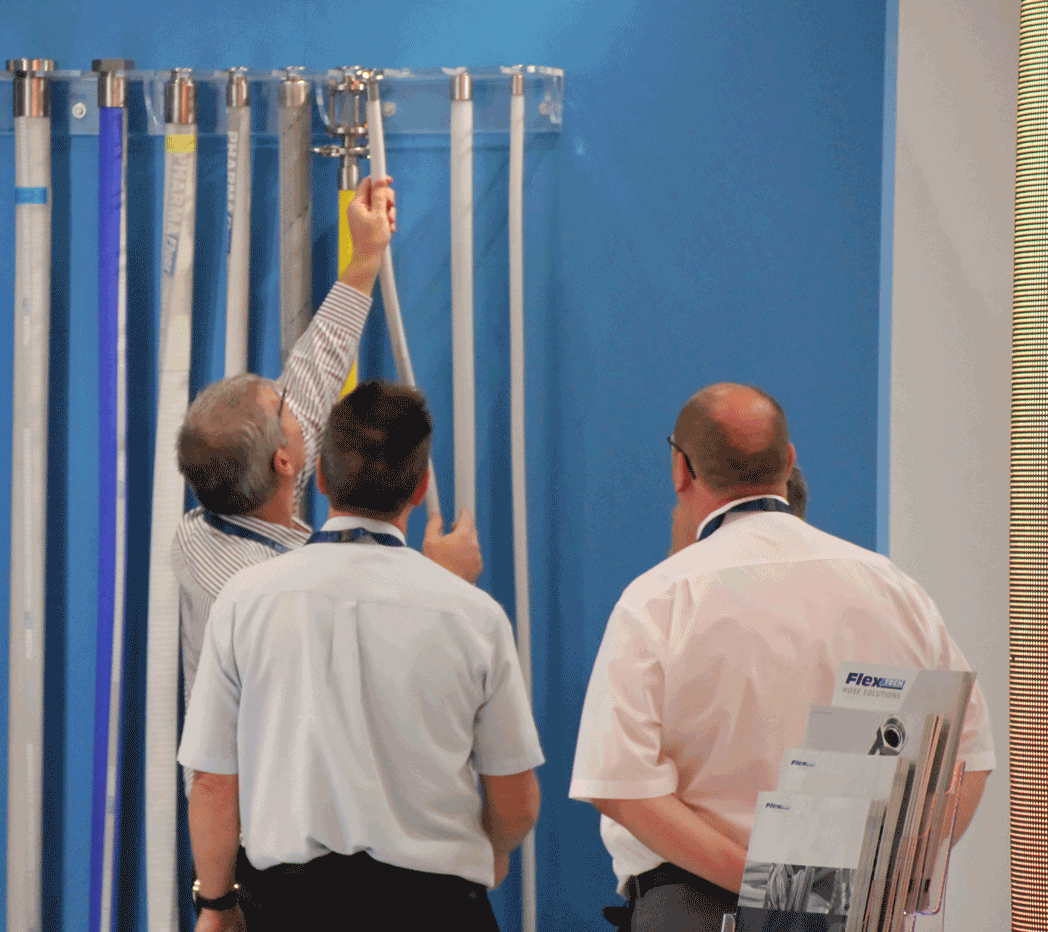
Our Experience
Our staff have been involved in the hose industry since 1982 and Flextech has grown up with the industry too since its incorporation in 2009. As the hose market has matured we’ve been able to develop a unique perspective on things. We understand the quirks of certain products, the suitability of specific materials and the engineering capabilities offered by individual manufacturing methods. This helps us know what’s required to deeply understand your needs and uncover all the hidden variables of your niche application that need to be brought into the equation.
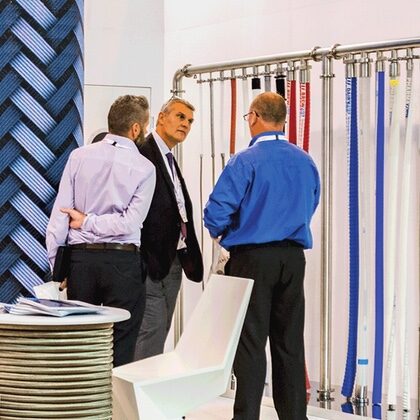
Hose Selection Guide: A Comprehensive Approach to STAMPED Criteria
Selecting the appropriate hose is crucial for maintaining efficient fluid transportation and ensuring the longevity of a system. To simplify the process and cover all essential aspects, we use the acronym STAMPED: Size, Temperature, Application, Material, Pressure, Ends of couplings, and Delivery (flow rate). Each element plays a vital role in determining the suitable hose for a given application. This document aims to expand on each criterion, providing valuable insights and detailed guidance to make informed decisions.
This universal criteria for hose assemblies, STAMPED, is a simple way of detailing the critical requirements that we need from you before we can design and build your hose assembly. At Flextech we will run through all these requirements with you before we begin manufacturing so the responsibility for success is not just up to you. Our specialising in designing and manufacturing flexible hose assemblies which will transport a given product efficiently and cost effectively from point A to point B is not as straight forward as you may think. Building a Hose Assembly is quite a complex task that can entail many intricate variables, (though not many people/companies are aware of this), therefore in order to improve the efficiency of the data identification process we have produced the following guideline.
This guideline will also help you check your existing hose applications and be more informed of critical requirements as the effects of having an incorrect hose installed can have costly consequences such as batch contamination, health and safety issues, premature hose failure and increased maintenance costs.
Size:
The hose's inside diameter is a critical factor to minimize pressure loss and prevent damage from media, cold or heat generation, vibration or flexing. To determine a replacement hose size for an existing hose, you can carefully measure the inside diameter. Before cutting your original assembly, record the overall assembly length and fitting orientation for building the replacement assembly. Pay attention to the hose's outside diameter (O.D.) too.
We need to know the length of the hose that you require in order to sufficiently reach its application. In order to determine the best size we need to know;
- The hose ID (internal diameter)
- The flow requirements
- The potential pressure loss considerations on long-length hoses
- The available end connections that can be fitted for your application
Temperature:
Replacement assembly selection must consider both the fluid and ambient temperatures. The chosen hose must withstand the system's minimum and maximum temperatures. Ensure that the hose's maximum temperature specification is continuous and not intermittent. Special caution is necessary when routing hoses near hot manifolds, and the use of heat shields may be advisable in extreme cases.
The temperature of the product can drastically reduce effective hose life if the hose is not designed with what it will convey in mind. In addition, the temperature of the surrounding hose environment can affect the way in which it will perform. For this reason, certain hoses are specifically designed and manufactured to withstand extreme operating temperatures of either heat or cold.
It is therefore crucial that the proposed hose temperature limits are always compared with the hose application that you intend to satisfy before placing an order.
Application:
The hose application is one of the most important factors to be considered when deciding the correct type of hose to use. As well as considering the temperature and pressure that your hose will be exposed to, also think about abrasion, oil, chemicals or any other variables which may affect the durability of the hose. Flextech can supply any hose required as long as we know exactly how the hose is to be used. It is possible for us to design a hose from scratch in order to increase the service life so don’t rule any possibilities out.
Thoroughly analyse the application's requirements and conditions to ensure proper hose selection. Consider factors such as:
- Hose usage location.
- Fluid and ambient temperatures.
- Hose construction.
- Equipment type.
- Fluid compatibility.
- Thread end connection type.
- Working and surge pressures.
- Environmental conditions.
- Suction application.
- Routing requirements.
- Compliance with government and industry standards.
- Handling of unusual mechanical loads.
- The need for non-conductive hose.
- Protection against excessive abrasion.
Material to be Conveyed:
Certain applications demand the transportation of specialized oils or chemicals, making it essential to select hoses compatible with the conveyed fluid. Pay attention to the hose tube, cover, couplings, and 'O' rings to ensure their compatibility with the fluid in use. Exercise additional caution when selecting hoses for gaseous applications like Freon and LPG.
It is important to understand that the material or product which travels through the hose is compatible with the compound that the hose is made from.
This is because many products, especially chemicals, can actually erode or wear away the hose inner wall which could in turn cause operating efficiency problems. It is, therefore, crucial to keep in mind fluid/product/hose compatibility.
If you are not sure which material or product is or isn’t suitable the best thing to do is to check our chemical compatibility chart.
Pressure:
System pressure should not exceed published working pressures. Pressure spikes beyond the specified working pressures can significantly shorten hose life. Avoid using hoses in applications with pressure spikes exceeding the published working pressures. Always adhere to the manufacturer's guidelines for optimal performance and safety.
Ends of Couplings:
Identify the end connections required for your application and consult the appropriate coupling chapters in the catalogue for specific part number selection. Proper coupling ensures a secure and leak-free connection, promoting overall system reliability.
Delivery (Flow Rate):
Assuming the same inside diameter as the original hose, it is essential to ensure the system is appropriately sized to efficiently transport fluid. If the system is new or modified, determine the hose inside diameter needed to achieve the required fluid volume flow using the nomographic chart.
Summary/Conclusion:
Selecting the correct hose involves considering various critical factors encapsulated by the STAMPED acronym: Size, Temperature, Application, Material to be conveyed, Pressure, Ends of couplings, and Delivery (flow rate). By understanding and addressing each aspect, you can make well-informed decisions, ensuring the hose's optimal performance, safety, and durability. Remember to consult hose specification tables, adhere to manufacturer guidelines, and exercise caution in gaseous or specialized fluid applications. Following these comprehensive guidelines will lead to the successful selection of hoses tailored to your specific needs and operational requirements.